STATE OF LVT SUSTAINABILITY
- Share
- Issue Time
- May 3,2016
Summary
LVT is a relative newcomer to the sustainability game. Like all vinyl products, it has been in more of a defensive mode because of controversy over its ingredients.
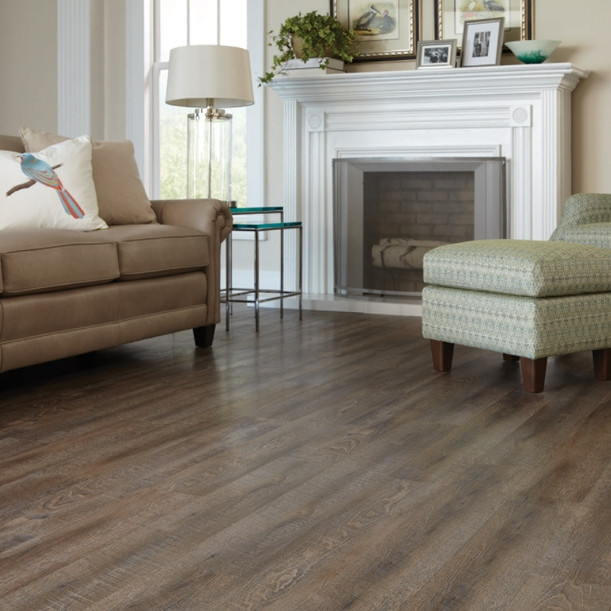
LVT is a relative newcomer to the sustainability game. Like all vinyl products, it has been in more of a defensive mode because of controversy over its ingredients. The most commonly used green certifications for vinyl flooring tend to cover indoor air quality and volatile organic emissions (like FloorScore and Greenguard). The multi-attribute certification, NSF-332, has also gained traction. For now, there are few manufacturer-specific environmental product declarations (EPDs). Health product declarations and ingredient lists are also not widely used.
Most of the environmental progress in LVT (and PVC flooring in general) over the last few years has been in the greening of additives. Vinyl flooring uses two types of additives for structural performance: plasticizers and stabilizers. The plasticizers convey elasticity to the product, making it bendable and malleable and giving it the necessary resilience to survive high foot traffic. Then there are the stabilizers, designed to prevent thermal decomposition when the material is heated.
In the past, stabilizers made of lead were more common, but these days it’s mostly tin. The bigger problem has been with the plasticizers, which for many years were made of phthalates (like DEHP and DOP) implicated in endocrine disruption and reproductive harm.
The industry first moved to phthalates with higher molecular weights (like DINP), the idea being that these molecules would be too big to leach from the PVC. However, the affiliation with the problematic phthalates proved to be too strong, so in the last couple of years, led by firms like Tarkett, manufacturers have started introducing phthalate replacements, including bio-based plasticizers and a terephthalate called DOTP.
With plastics in general, landfilling is a big issue, because that material is essentially lost forever, a poor strategy for materials made of diminishing fossil fuel supplies. PVC belongs to a class of polymers called thermoplastics, which essentially means that they can be remelted and turned into new product. Some thermoplastics survive the process better than others. PVC, like nylon, is one of the better thermoplastics.
This thermoplastic quality makes PVC a good candidate for recycling and reclamation, but so far the industry has not seen much post-consumer recycled material. For PVC to become a valid sustainable product, it will have to be kept out of the waste stream, and this is one of the issues manufacturers are currently struggling with.